Introduction: Clarifying the Alphabet Soup of Manufacturing Systems
Modern manufacturing is under intense pressure. Customers expect faster delivery, lower costs, and higher quality. To keep up, manufacturers are investing in digital tools to improve how they plan, execute, and manage production. But with so many software systems—MES vs ERP vs MRP—it’s easy to get lost in the jargon.
Each system plays a distinct role in your operation, but their functions often overlap, leading to confusion. This article clears the fog. We explain the purpose of each system, how they interact, and how to choose the right mix for your factory. Whether you’re scaling operations or simply trying to gain more control over your shop floor, understanding MES, ERP, and MRP is critical to getting your next investment right.
What is MRP?
Material Requirements Planning (MRP) is the foundation of manufacturing planning. Its primary goal? Making sure you have the right materials, in the right quantities, at the right time.
MRP systems take a Master Production Schedule (MPS) and break it down using the Bill of Materials (BOM), current inventory, and lead times. The system calculates net material requirements and generates purchase or production orders to ensure materials are available when needed.
Key MRP Functions:
Inventory Management: Prevents shortages or overstock by matching inventory to the production schedule.
Production Scheduling: Ensures materials and components are ordered or built in time to meet planned production dates.
MRP evolved into MRP II in the 1980s, expanding into capacity planning and linking with procurement and finance. Today, most modern ERP systems include MRP logic by default.
Ideal Use Cases:
Factories with complex BOMs or many subassemblies.
Manufacturers needing better inventory control or supply chain coordination.
Limitations:
Dependent on accurate data (“garbage in, garbage out”).
Lacks real-time visibility and execution control.
What is MES?
A Manufacturing Execution System (MES) controls and monitors real-time activities on the shop floor. While ERP and MRP focus on planning, MES is all about execution.
MES connects operators, machines, and materials to ensure production runs as expected. It tracks every part, every machine state, and every operator action—right as it happens.
Key MES Capabilities:
Work Order Execution: Translates schedules into operator tasks with digital instructions.
Real-Time Data Collection: Tracks machine status, quality checks, cycle times, and more.
Quality & Compliance: Enforces quality gates, traceability, and standardized workflows.
Performance Metrics: Reports downtime, scrap, and OEE to support continuous improvement.
MES lives on the ISA-95 Level 3 layer—between enterprise planning (ERP) and control systems (PLCs, SCADA). It’s where the digital plan becomes physical reality.
Ideal MES Use Cases:
High-mix, complex discrete manufacturing.
Regulated industries requiring traceability and audit trails.
Plants aiming to reduce downtime, scrap, and rework.
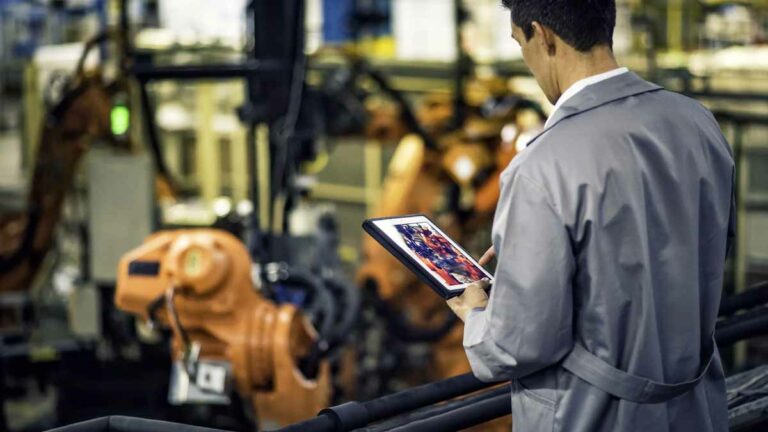
What is ERP?
Enterprise Resource Planning (ERP) is the business system that ties everything together. ERP manages accounting, HR, sales, purchasing, and often manufacturing planning too. Think of it as the business’s central nervous system.
At its core, ERP:
Consolidates data across departments.
Automates core business processes.
Provides decision-makers with visibility across the enterprise.
Most ERPs include an MRP engine, which handles production planning. But they typically don’t manage real-time shop floor activity—that’s MES’s job.
Key ERP Capabilities:
Integrated Business Processes: Finance, procurement, HR, sales, and supply chain in one system.
High-Level Planning: Manages forecasts, orders, costs, and schedules.
Scalable Architecture: Supports multi-site, global operations.
Limitations:
Costly and time-consuming to implement.
Not designed for minute-by-minute production control.
Comparison: MES vs ERP vs MRP
Let’s compare these systems side by side:
- ERP
- MRP
- MES
ERP | MRP | MES | |
Primary Role | Enterprise-wide coordination | Material and schedule planning | Shop floor execution and control |
Data Focus | Business and transactional data | BOMs, inventory, forecasts | Real-time operational data |
Time Horizon | Past, present, future | Near-future | Real-time |
Integration Layer | Top floor | Mid-layer (within ERP) | Shop floor |
Typical Users | Executives, planners, back office | Planners, schedulers | Operators, supervisors, quality |
Each system operates in a different time and control layer. MRP plans the work. MES executes it. ERP aligns all resources and tracks the outcome.
MES vs ERP vs MRP: Where They Overlap and Why Integration Matters
While ERP, MES, and MRP serve different roles, their true strength emerges when they are integrated. The first major area of overlap is production scheduling. ERP (through its MRP engine) often sets high-level production timelines—for example, what needs to be completed each day. MES then refines that plan, breaking it into precise tasks for specific machines and operators. Integration ensures both systems stay aligned. If a delay occurs on the shop floor, MES can push updates back to ERP, prompting real-time rescheduling upstream.
The second critical overlap is inventory and WIP tracking. ERP tracks finished goods and raw materials at a warehouse level, while MES handles the materials in process—what’s being consumed, where batches are, and what’s nearly done. Without integration, WIP status might remain invisible to ERP users. But when MES and ERP talk to each other, production data flows seamlessly from one to the other, reducing errors and improving inventory accuracy.
The third area is quality management. MES enforces real-time checks during production—measuring tolerances, confirming operator steps, and recording failures. ERP may also record quality outcomes, such as returns or audit logs. If MES and ERP aren’t integrated, quality events might be logged twice or inconsistently. A well-integrated system lets MES capture the raw data and share it upstream with ERP for reporting, compliance, and customer documentation.
In all three areas, integration closes gaps and eliminates silos. The result is a responsive, data-driven manufacturing system where plans are informed by reality, and execution is guided by the broader business context.
Choosing What Your Factory Needs
Choosing the right mix of systems isn’t just about software—it’s about solving the most pressing problems in your factory. Start by assessing the complexity of your production process, your company’s size, and your long-term goals.
Company Size and Maturity
Smaller manufacturers may begin with spreadsheets or basic accounting tools. As operations grow, an ERP with built-in MRP is often the first logical step. It helps manage orders, inventory, and costs across departments. Larger or more mature companies, especially with multiple facilities, benefit from adding MES to improve visibility and coordination at the shop floor level.
Manufacturing Complexity
Simple assembly lines may not require MES right away. But as product mix grows or regulatory oversight increases, MES becomes more valuable. If you’re managing custom work, tight tolerances, or complex routing, MES can ensure consistency and traceability.
Industry Requirements
Some sectors—like aerospace, medical devices, and pharmaceuticals—require detailed documentation and traceability. MES is often essential in these environments. It can enforce process steps, log operator actions, and ensure every product meets standards. ERP alone rarely meets those operational compliance needs.
Key Pain Points
If your main challenge is knowing what to order and when, MRP (via ERP) can resolve that. If you’re struggling with downtime, quality escapes, or real-time status, MES is likely the better place to start. Identify the bottlenecks: do they stem from business process misalignment, or from execution failures on the floor?
Budget and Implementation
MES systems often require less time and budget to implement than ERP, and can deliver ROI quickly. If funding is limited, some manufacturers deploy MES first to improve performance, then invest in ERP once the business has grown.
Integration with Existing Tools
Don’t overlook your current software stack. If you already use QuickBooks, spreadsheets, or a basic ERP, consider how easily a new system will connect. Many MES platforms (including no-code options like PINpoint) offer plug-and-play integration with leading ERP systems.
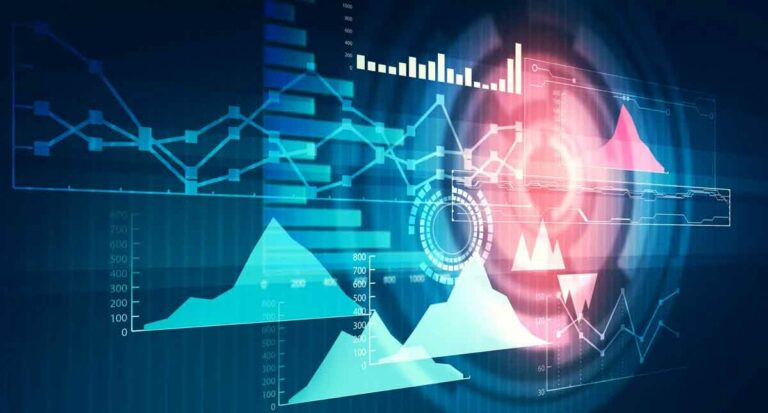
Industry Scenarios
Automotive Supplier: A large Tier 1 supplier receives monthly production orders from OEMs. The ERP system (SAP) handles high-level scheduling and procurement. MRP plans out what components to order and when, while MES sequences tasks on each assembly line, guides operators through torque checks, and captures test results. This integration allows the company to meet strict customer delivery targets while maintaining ISO-certified traceability.
Small Job Shop: A 50-person custom fabrication shop installs a cloud ERP to manage quotes, sales orders, purchasing, and basic inventory. MRP within the ERP helps avoid material shortages and improves promise dates. As they grow, they add a lightweight MES module to capture job progress and operator input. This phased approach lets them gain efficiency on a limited budget, without disrupting current operations.
Pharmaceutical Manufacturer: A biotech firm uses ERP to manage long-lead raw materials and financials. The MES ensures each batch follows strict protocols, logs environmental conditions, and enforces in-process quality checks. Operators interact with on-screen instructions, and each batch record is automatically generated for FDA compliance. Integration between MES and ERP ensures accurate lot tracking, inventory adjustments, and cost control.
Conclusion: Getting the Right Systems, in the Right Order
MES vs ERP vs MRP? These systems are not rivals. They’re partners in the same goal: improving production.
MRP helps you plan material needs.
MES helps you execute production efficiently.
ERP helps you coordinate all business processes.
Most factories benefit from using all three. The right implementation order depends on your biggest pain point—whether that’s planning, execution, or coordination. And the real value emerges when these systems are integrated to work as one.
As smart manufacturing becomes the norm, understanding this software stack is essential to staying competitive. The future belongs to manufacturers who connect their top floor to the shop floor—and use real-time data to drive operational excellence.