Introduction to Quality Management Systems (QMS)
A Quality Management System (QMS) is a formalized framework that governs how a business manages and improves quality. It helps manufacturers deliver consistent results, meet customer expectations, and comply with industry standards. By embedding quality into every process and every product, a QMS helps build a culture of accountability and continuous improvement.
Defining a QMS
At its core, a QMS is a structured approach to defining, documenting, executing, and improving an organization’s quality-related processes. It covers how a manufacturer handles product specifications, monitors process performance, controls documentation, resolves issues, and implements corrective action. Unlike ad hoc quality checks, a QMS connects people, procedures, tools, and data into a unified system focused on delivering quality outcomes.
Why Manufacturers Rely on QMS
The need for a QMS becomes obvious when operations scale or when compliance becomes critical. Manufacturers adopt QMS frameworks to eliminate variability, reduce waste, and make quality measurable. When properly implemented, a QMS does more than just meet minimum standards—it supports faster training, better product traceability, and more reliable outcomes, even across high-mix production environments.
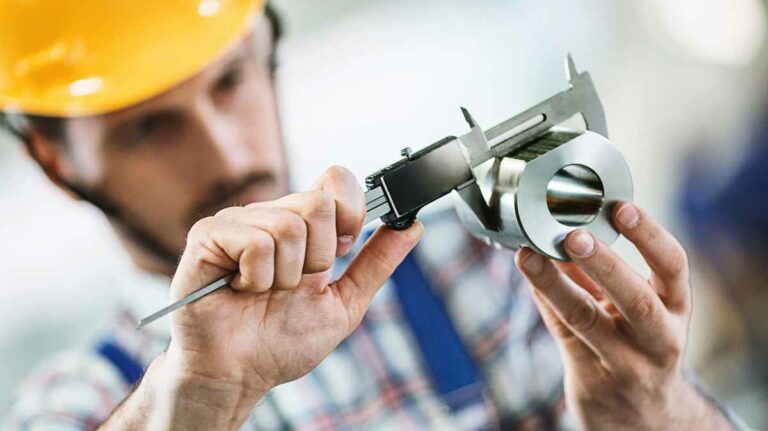
What Makes Up a QMS?
A modern QMS consists of several key elements that work together to enforce quality at every stage of production:
First, the quality policy and objectives define what quality means for the organization and establish clear goals for performance. These guide the structure and intent of the system.
Next, document control ensures that every procedure, checklist, and specification is up to date and version-controlled. This prevents confusion on the floor and ensures everyone works from the latest information.
Process control defines how manufacturing activities are carried out. It includes parameters for inputs, required equipment, tolerances, and output specifications. It also defines what to do when a step cannot be completed as intended.
A critical part of the system is the Corrective and Preventive Action (CAPA) process. CAPA ensures that when something goes wrong—or when something nearly goes wrong—it is documented, investigated, and resolved at the root cause level.
To keep the QMS running effectively, internal audits are conducted regularly. These audits assess whether people are following procedures and whether those procedures still achieve the desired results.
Management plays a key role through the management review process. Here, leadership reviews performance data, evaluates risks, and makes decisions on how to allocate resources or revise quality goals.
Lastly, training and competency tracking ensures that every employee has the skills and knowledge required to perform their tasks according to quality standards. This includes initial training, skills refreshers, and updates when procedures change.
Aligning with Global Standards
Manufacturers typically align their QMS with international standards. These include:
ISO 9001, which provides a broad framework for quality management and is applicable across industries.
IATF 16949, used specifically in the automotive industry to address sector-specific requirements.
AS9100, which extends ISO 9001 for aerospace and defense manufacturers.
ISO 13485, which applies to medical device manufacturing and emphasizes risk management and product traceability.
FDA 21 CFR Part 820, a regulation that outlines quality system requirements for medical devices sold in the United States.
Certification or alignment with these standards helps organizations meet customer requirements, reduce liability, and gain access to regulated markets.
Key Benefits of a QMS
A properly implemented QMS delivers both operational and strategic benefits. At the operational level, it reduces variation by ensuring that every worker follows a standardized process. This leads to more consistent outcomes and fewer defects.
Strategically, a QMS builds a foundation for scalable, repeatable quality. It enables organizations to identify trends, take preventive action, and support lean manufacturing initiatives. During audits, a strong QMS provides traceable records and a clear audit trail, reducing the time and cost of demonstrating compliance.
Importantly, a QMS also contributes to customer satisfaction. When buyers know that your processes are controlled and documented, they are more confident in your ability to meet their specifications consistently.
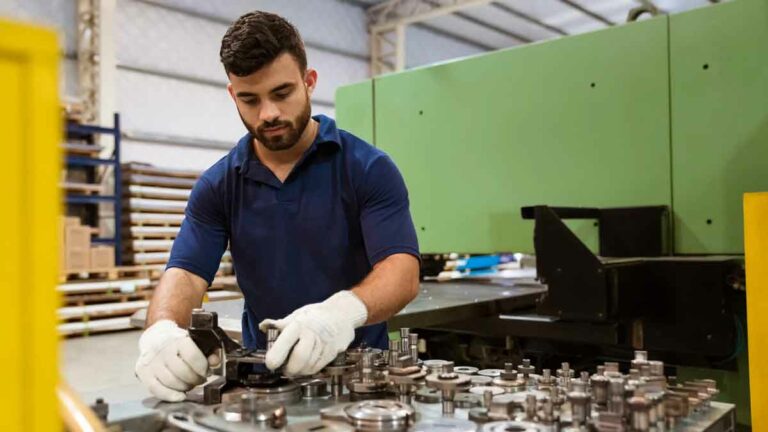
QMS vs Quality Control: What’s the Difference?
While quality control (QC) is often associated with inspecting finished products, a QMS takes a much broader and more proactive approach. QC focuses on detecting defects after production. QMS, in contrast, is about designing and managing the processes that prevent defects from occurring in the first place.
Think of QC as the final check. A QMS is the system that ensures everything before that final check is done right.
How a QMS Fits into Modern Manufacturing
In discrete manufacturing, QMS practices are deeply embedded in every department:
Engineering defines what quality looks like at the design level.
Procurement ensures that suppliers meet specified standards and deliver consistent components.
Production follows work instructions and uses standardized tools and materials to maintain process control.
Inspection uses calibrated equipment and documented criteria to validate product quality.
These departments are linked through documented procedures, shared data, and regular communication—facilitated by the QMS.
The Shift to Digital Quality Management
Many manufacturers are now transitioning from paper-based systems to digital QMS platforms. These systems offer electronic document control, real-time data capture, and automated alerts for non-conformance. They also provide dashboards and reports that help managers identify trends and respond faster to problems.
Digital QMS tools are often integrated with other systems like Manufacturing Execution Systems (MES) and Enterprise Resource Planning (ERP), allowing for seamless data exchange and greater transparency.
QMS in Regulated Manufacturing
In regulated industries, a QMS isn’t just useful—it’s mandatory.
For example, medical device manufacturers in the U.S. must follow FDA 21 CFR Part 820, which requires documentation of every step in the manufacturing and quality process. Automotive suppliers must meet IATF 16949 to do business with OEMs. In aerospace, AS9100 demands rigorous documentation, traceability, and risk management practices.
Without a QMS that meets these requirements, companies cannot compete or stay compliant.
The Future of QMS: Predictive, Not Just Preventive
As more factories adopt Industry 4.0 technologies, QMS platforms are becoming smarter. Sensors and IoT devices can detect early signs of variation. Artificial intelligence can analyze trends across lines or shifts. This enables predictive quality management—where problems are prevented before they occur, not just caught after the fact.
Manufacturers who invest in modern QMS tools will be better positioned to maintain quality in high-mix, high-variability environments, while also reducing waste and increasing agility.
Conclusion
A Quality Management System is essential for manufacturers who want to compete on quality, meet industry standards, and satisfy customer demands. By structuring how quality is defined, measured, and improved, a QMS turns quality from a reactive function into a strategic asset.
For manufacturers serious about continuous improvement, compliance, and operational excellence, a QMS is not just important—it’s indispensable.