Introduction to MES and Manufacturing Work Instructions
Manufacturing Work instructions are essential to factory operations. They guide operators step-by-step, ensure quality, and support compliance. But in many plants, instructions still exist as static documents—printed on paper, pinned to boards, or buried in file systems. That’s where a Manufacturing Execution System (MES) adds value.
MES transforms work instructions from passive reference material into active, dynamic tools. It delivers the right instruction to the right operator, at the right time. It verifies that steps are completed correctly. And it captures data to support traceability, audits, and continuous improvement. In this article, we’ll examine how MES improves work instructions—and share real-world examples from manufacturers who’ve made the shift.
Dynamic Delivery of the Right Instruction
MES connects work instructions directly to production orders and shop floor activities. When an operator logs into a workstation, the MES identifies the task and displays the correct instruction. This ensures that:
- Instructions match the specific product version or configuration.
- Operators see only what’s relevant to their task.
- Updates are instant and universal—no outdated paper copies or conflicting versions.
This context-sensitive delivery reduces errors and confusion. For example, a plant that builds medical devices may produce the same item in multiple sizes or specifications. MES ensures that each variation has its own validated instruction, reducing the risk of mix-ups.

Guided Execution and Verification
In a paper-based environment, it’s easy to skip steps or misinterpret instructions. MES enforces the correct sequence. Operators must confirm each step—by checking a box, entering data, scanning a barcode, or completing a digital form—before moving on.
This guided execution ensures that nothing is missed. If a torque value is out of range or a component is misaligned, the MES can block progress and prompt corrective action. For example, at one aerospace manufacturer, MES prevented 63% of assembly errors by requiring digital confirmation of each process.
MES also integrates with sensors, tools, and smart devices. A digital torque wrench can send values directly to the MES. Vision systems can verify part placement. This machine-verified feedback increases accuracy while reducing manual documentation.
Integrated Quality and Compliance
MES helps manufacturers meet quality and regulatory requirements. Every instruction is linked to revision history, approval workflows, and audit trails. This is especially important in industries like automotive, aerospace, electronics, and life sciences.
For example:
- MES tracks who performed each step, when, and on which machine.
- It records all exceptions, such as skipped steps or deviations.
- It stores inspection results and measurement data in context.
During audits, manufacturers can quickly show compliance. If a defect occurs, MES helps trace it back to the exact build, operator, and material lot. This level of accountability is difficult to achieve with paper or disconnected systems.
Real-Time Updates and Continuous Improvement
Manufacturing Work Instructions change—whether due to design revisions, process updates, or quality improvements. In a manual system, distributing and enforcing these changes is slow and error-prone. MES solves this by updating instructions centrally and pushing changes to all relevant workstations.
When an engineer uploads a new version, the MES replaces the old one immediately. It can also require re-training or acknowledgment from affected staff. This improves change control and ensures that updates are followed.
MES also supports data-driven improvements. By tracking how long each step takes, how often issues occur, and where rework is needed, it helps identify opportunities to optimize work instructions. For example, if operators consistently pause at Step 6, it may indicate unclear language or missing visuals.
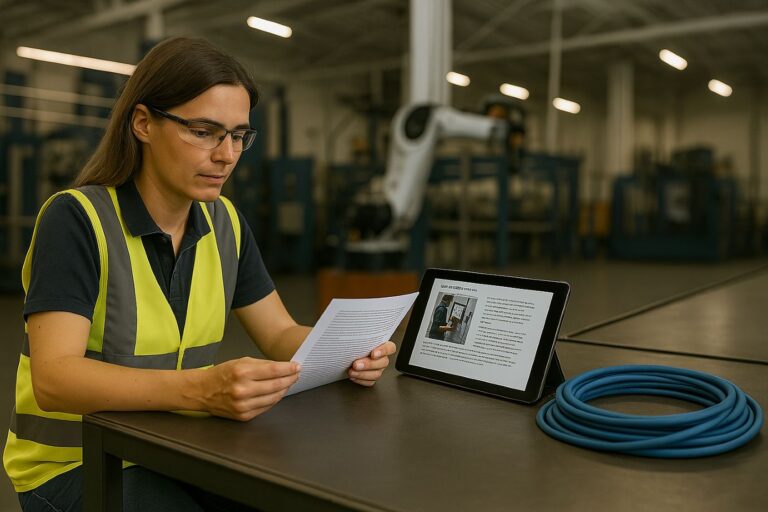
Supporting Workforce Development
MES-based instructions reduce training time. New employees follow clear, guided workflows instead of relying on tribal knowledge. Some systems adjust instructions based on user skill level. A novice might see detailed instructions with images and safety reminders, while an experienced user sees a concise checklist.
This adaptability helps manufacturers onboard faster, cross-train more easily, and maintain quality during labor shifts. In a case study from Tulip, a facility using digital work instructions reported 50% faster training time and higher job satisfaction.
Case Studies: Manufacturing Work Instructions and MES in Action
CMP Advanced Mechanical Solutions
CMP adopted MES with integrated work instructions to support its complex assembly operations. The company cut training time in half and increased quality. Operators no longer relied on paper binders or outdated PDFs. Instead, they accessed up-to-date instructions on tablets, tailored to the exact build.
Boeing
In wire harness assembly, Boeing used AR-based instructions connected to MES. Workers followed step-by-step visual cues through smart glasses. This approach improved first-pass yield by 90% and cut wiring time by 25%.
Siemens
Siemens deployed MES across multiple plants to digitize operations. Work instructions were synchronized with product configurations and quality checks. One site reduced energy consumption by 12% by linking instructions with MES-triggered power settings.
Conclusion
MES elevates manufacturing work instructions from static documents to intelligent production tools. It ensures accuracy, enforces sequence, integrates quality checks, and adapts to changes in real time. More importantly, it captures data to support compliance and continuous improvement.
For manufacturers, this means fewer errors, faster training, stronger traceability, and higher output. In a competitive market where quality and agility matter, MES-enabled work instructions are no longer optional—they are essential.
As the next step, manufacturers can explore how these digital instructions tie into broader initiatives like smart tools, predictive analytics, and AI-driven decision support. But it starts with one transformation: putting the right instructions in the right hands, at the right time.