Common Use Cases for MES in Automotive Manufacturing
Manufacturing Execution Systems (MES) are critical to managing modern automotive production. With increasing demand for electric vehicles, greater product variation, and tighter regulatory requirements, manufacturers need real-time control and visibility across the plant floor. MES software helps automotive factories run more efficiently, maintain quality, and respond quickly to production issues.
This article explores the most common MES use cases in automotive manufacturing. Each one reflects real-world problems that MES helps solve, from tracking components to enforcing quality standards. The use cases are applicable to both automotive OEMs and component manufacturers.
Overview of MES Capabilities in Automotive
Automotive manufacturers operate high-speed, high-volume production environments. MES platforms bridge the gap between enterprise-level planning systems (like ERP) and plant floor operations (like PLCs and SCADA). Typical MES functions include:
Real-time production tracking
Quality control and non-conformance handling
Traceability and product genealogy
Digital work instructions and operator guidance
Line performance monitoring and OEE measurement
Integration with warehouse and material systems
These features work together to improve control, consistency, and responsiveness across the production lifecycle.
1. Real-Time Production Monitoring and Downtime Tracking
One of the most common uses of MES in automotive plants is real-time production monitoring. MES collects data from machines, sensors, and workstations to provide a live view of what is happening on the line.
This data helps teams spot issues quickly, respond to bottlenecks, and reduce unplanned downtime. MES also logs the reasons for downtime—whether it’s due to machine faults, material shortages, or operator delays.
You can read a real case study for MES in automotive from a PINpoint user here: Supercar Engine Assembly Case Study
2. Quality Management and Non-Conformance Handling
MES plays a key role in automotive quality assurance. It helps enforce inspections, log defects, and track resolutions. The system ensures that quality checks are not skipped and that failed checks trigger predefined responses.
A common example is enforcing correct torquing of bolts during assembly. MES can control the operation to ensure the correct number of tightening operations are conducted, using the correct tool with the correct settings. If an operator deviates from the prescribed process or experiences a fault, this can be logged and associated with the part or product in build.
MES also supports Statistical Process Control (SPC) and provides historical quality data for analysis.
You can ready about results possible with PINpoint MES, including reducing bolted joint failures by 94% on our results page.
3. Traceability and Lot Genealogy
Traceability is essential in the automotive industry. MES records the full history of each vehicle, including component serial numbers, operator actions, test results, and workstation IDs.
This level of detail is critical for recalls, warranty claims, and compliance audits.
Because it is optimized for serialized production, PINpoint MES is able to link each VIN to specific components used during assembly. If a supplier recall is issued, only affected vehicles can be identified and serviced.
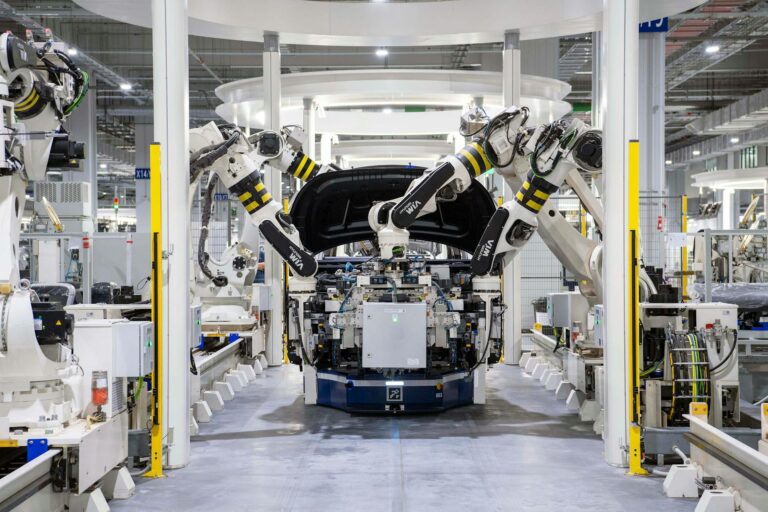
4. Digital Work Instructions and Operator Guidance
MES provides visual work instructions that guide operators through each step of the build process. This reduces errors, especially for new or temporary workers.
Instructions can include diagrams, photos, and verification prompts. The system can also prevent the operator from proceeding if a critical step is skipped.
Example: In EV battery pack assembly, MES guides the technician through insulation checks, cell alignment, and torque settings with images and confirmation prompts.
Read our full article on the benefits of digital work instructions with MES here: How MES Improves Manufacturing Work Instructions
5. Operator Accountability and Performance Tracking
MES enables detailed tracking of operator activities at each workstation. This includes task completion times, error rates, training status, and adherence to standard operating procedures. By associating specific actions with individual employees, MES promotes accountability and helps identify training needs.
Supervisors gain visibility into who performed each task, how long it took, and whether any deviations occurred. This data can inform performance reviews, continuous improvement initiatives, and safety compliance.
Example: MES logs that a specific operator skipped a required verification step during dashboard installation. The system flags the deviation, notifies the team lead, and ensures corrective action is documented.
6. Production Scheduling and Line Balancing
Automotive manufacturers often run mixed-model production on the same line. MES helps manage the complexity by dynamically adjusting schedules based on actual conditions.
It provides valuable insights to managers and supervisors to help them balance workloads, minimize changeover times, and meet delivery deadlines.
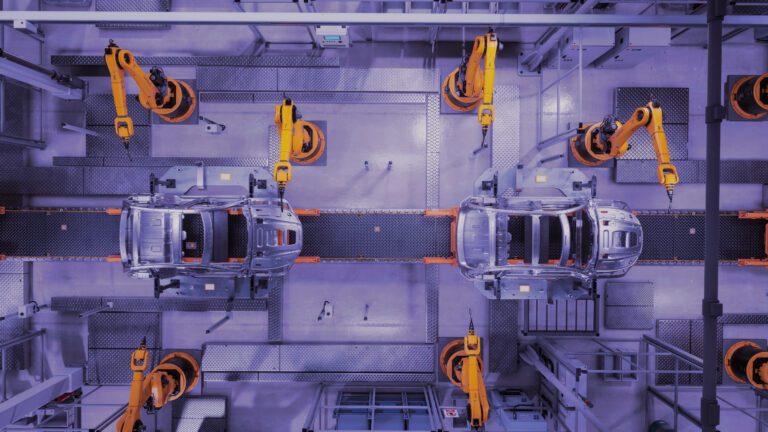
7. Regulatory and Customer Compliance Reporting
OEMs and Tier 1 suppliers must meet global standards like IATF 16949 and customer-specific requirements. MES generates detailed reports and audit trails that demonstrate compliance.
These records are essential during quality audits or in response to customer claims.
Example: MES stores torque values and inspection results for each fastener in the powertrain, providing verifiable proof of process compliance.
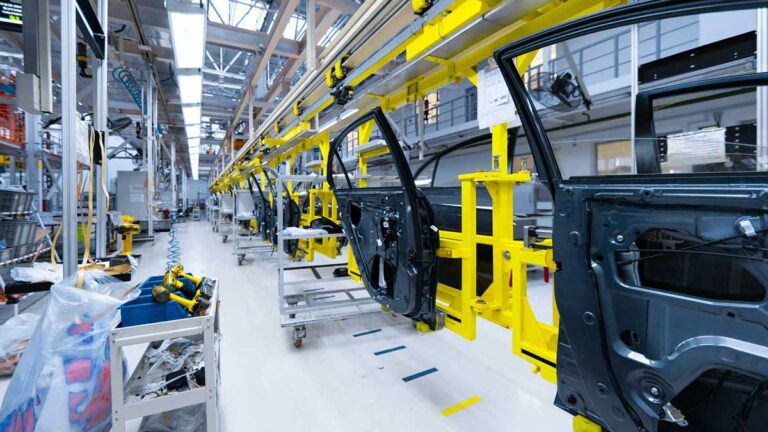
Conclusion: Why MES Is a Must-Have in Automotive Manufacturing
MES supports automotive manufacturers in meeting the demands of high-volume, high-precision production. From quality control to compliance reporting, its role spans every stage of the build process.
By implementing MES use cases like the ones above, automotive plants can boost efficiency, reduce errors, and build trust with OEMs and regulators.
Related Reading:
Interested in optimizing your automotive plant with MES? Why not book a demo or request a meeting with a PINpoint expert today?