Introduction
Manufacturing Execution Systems (MES) have become indispensable to modern factory operations. They track, control, and document the transformation of raw materials into finished goods, acting as the digital core of production. But the value an MES delivers is only as strong as the quality of data it receives and generates. Without clear governance and a trusted foundation of master data, MES platforms can automate chaos rather than prevent it.
This article examines why MES, data governance, and master data management (MDM) must be treated as a single strategic imperative rather than siloed initiatives. It also outlines how manufacturers can structure their approach to ensure the integrity, consistency, and business value of production data—especially in highly regulated or quality-sensitive industries.
The MES as an Execution Engine: Fueled by Data
Today’s MES is no longer just a shop-floor tracker. It integrates real-time data from machines, people, and processes to deliver visibility, enforce quality, and enable traceability. It connects to enterprise-level systems like ERP and Product Lifecycle Management (PLM) tools, as well as to plant-floor equipment through industrial protocols and IoT platforms.
This makes the MES a central actor in the production ecosystem. But it’s only effective if the data that flows through it is governed, structured, and trustworthy. MES is not intelligent on its own—it depends on having the right data in the right format at the right time.
Consider a production order released to the MES. To execute that order correctly, the system needs access to the approved Bill of Materials (BoM), process routing, and recipe parameters. It also needs to know which equipment is available, what skillsets are required, and which quality checks are mandatory. If any of this data is incorrect, outdated, or missing, the MES may execute flawed instructions—leading to scrap, non-conformances, or audit failures.
Data Governance: Managing Manufacturing Data as a Strategic Asset
Data governance in manufacturing is the set of roles, processes, policies, and standards that ensure data is accurate, consistent, secure, and usable across its lifecycle. It’s not an IT project. It’s a business discipline—often overlooked until a failure forces attention.
In an MES environment, governance defines who owns each data type, how it is created and maintained, and who has authority to make changes. For example:
A process engineer may be the steward of routing data.
A quality supervisor owns the rules for quality inspections.
A plant manager is responsible for the accuracy of operational performance data.
Data governance also enforces access controls and audit trails. Sensitive data—like process parameters or equipment setpoints—must be version-controlled, accessible only to authorized personnel, and traceable. These controls are not just best practice; they are required in regulated industries to meet FDA, ISO, or GxP requirements.
By formalizing ownership and accountability, governance prevents the ambiguity that leads to untrusted data. It transforms the MES from a passive recorder into an active system of control and compliance.
Master Data Management: Enforcing a Single Source of Truth
While governance defines the rules, Master Data Management (MDM) ensures the rules are enforced across the most critical data domains. In manufacturing, these domains include:
Product master: part numbers, specifications, BoMs, routings
Material master: raw material IDs, supplier info, units of measure
Equipment master: asset capabilities, calibration dates, maintenance history
Personnel master: operator qualifications and certifications
Process master: approved manufacturing recipes and standard operating procedures
Many of these data types span multiple systems. A BoM might be created in PLM, transferred to ERP for planning, and consumed by MES for execution. Without MDM, each system may have its own conflicting version, with no guarantee of accuracy.
MDM solves this by establishing a “golden record”—a single authoritative version of each master data entity. Whether implemented via a central hub or a synchronization model, MDM ensures that MES and other systems work from the same data foundation.
This is particularly important for recipe data and routings. In process manufacturing, even a slight deviation in parameters can lead to quality issues. MDM tools embedded in MES can enforce version control and approval workflows, preventing unauthorized edits and ensuring that only the validated version is executed.
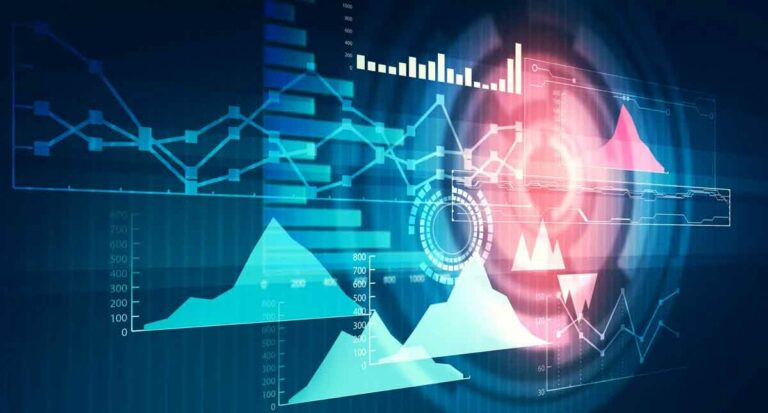
Integration with ERP and MRP: Where Overlap Requires Precision
MES typically integrates upstream with ERP and MRP systems. ERP plans what needs to be produced. MES handles how it’s made. But the handoff between systems requires governance and integration discipline.
A production order flows from ERP to MES, along with associated master data—product specs, materials, and routing. MES then executes the work, capturing real-time data on WIP, quality checks, and machine performance. After execution, MES reports back production quantities, consumption, and exceptions.
This integration creates several critical overlaps:
Inventory tracking: ERP tracks warehouse inventory; MES tracks shop-floor WIP. Without alignment, material counts diverge.
Scheduling: ERP provides macro-level plans; MES dispatches and adjusts in real time. If changes aren’t synchronized, schedules can conflict.
Quality records: MES captures granular quality events; ERP logs batch outcomes. Both must share a consistent view for compliance and customer communication.
Governance ensures that one system is designated as the system of record for each data type. Integration ensures that updates flow automatically, eliminating manual re-entry or duplication. Frameworks like ISA-95 define roles and data boundaries between MES and ERP, creating a standards-based foundation for synchronization.
Compliance and Traceability: Where Governance Pays Off
In regulated industries, MES is the backbone of traceability. It captures the complete genealogy of each product: what material was used, what equipment was involved, who performed each step, and what results were recorded.
But to satisfy regulators, that data must be complete, tamper-proof, and attributable. This is where data governance becomes indispensable.
MES platforms designed for compliance include features such as:
Electronic signatures at key steps (e.g. QA approval, batch release)
Audit trails that record every change to critical data, with time, user, and reason
Standard operating procedures embedded into workflows, enforcing consistency
When governed well, the MES becomes the primary evidence for proving compliance with standards like FDA 21 CFR Part 11, ISO 9001, or GAMP 5. It also accelerates audits, enabling fast retrieval of validated records rather than manual document searches.
A Three-Legged Stool: MES, MDM, and Governance
MES, MDM, and data governance are best understood not as separate systems but as three legs of a stool. If any one is weak or missing, the factory’s data infrastructure becomes unstable.
MDM feeds MES: The MES cannot execute reliably without trusted master data.
MES generates data: But without governance, that data cannot be trusted.
Governance guides both: It defines the roles, policies, and controls that give MDM and MES their structure and value.
Manufacturers who invest only in MES often experience disappointment. The system is installed, but expected benefits—like improved OEE, reduced scrap, or better decision-making—fail to materialize. The root cause is usually poor data.
Investing in governance and MDM is not overhead. It’s the enabling foundation for realizing MES value.
Strategic Recommendations
For manufacturers seeking to implement or optimize MES in a modern environment, the following principles apply:
Treat data as a product, not a byproduct. Production data should be clean, complete, and fit for purpose, just like any other deliverable.
Establish governance early. Before the MES goes live, define data ownership, create policies, and assign stewards.
Invest in MDM tools and processes. Focus especially on process master data, where change control is critical.
Use standards for integration. Leverage ISA-95 and structured APIs to create clarity between MES and ERP.
Design with compliance in mind. Make sure your MES can support audit trails, signatures, and SOP enforcement from day one.
Conclusion
A modern MES does more than monitor machines. It orchestrates a complex network of data, connecting planning with execution and transforming factory events into business intelligence. But to function effectively, it requires strong data governance and master data management.
Together, MES, MDM, and governance form the foundation of the data-driven factory. They ensure that every decision, action, and record is built on trusted information. In a competitive, regulated, and increasingly digital world, this foundation is not optional. it’s mission-critical.