Introduction
Modern manufacturing leaders are under pressure to reconcile two competing forces: the need for agile production planning and the reality of executing those plans on a complex, ever-changing shop floor. This divide—between high-level strategic scheduling and low-level execution—is where many systems fall short. But when Advanced Planning and Scheduling (APS) systems and Manufacturing Execution Systems (MES) are integrated, manufacturers gain a closed-loop control system capable of responding to real-world events in real time.
This article explains how APS and MES differ, how they complement each other, and why their integration is becoming a cornerstone of digital manufacturing strategies. It also explores the architectural decisions and governance considerations that determine whether this integration delivers lasting value.
The Roles of APS and MES
APS systems generate optimized production schedules based on real-world constraints. These constraints include machine capacity, operator availability, material inventory, and order due dates. The output is a feasible plan that aligns production with customer demand and business goals.
MES, by contrast, lives on the factory floor. It receives work orders, tracks progress, enforces process compliance, and captures performance data. While APS is the strategic brain, MES is the operational nervous system. Together, they create a powerful feedback loop between planning and execution.
The challenge arises when these systems are implemented separately. A standalone APS may generate an ideal schedule, but if MES doesn’t have real-time status data—or worse, has outdated or conflicting data—the plan quickly becomes obsolete. Similarly, MES without APS lacks a forward-looking engine to optimize how production should unfold.
Native Integration vs Standalone Scheduling Tools
One of the most important choices manufacturers face is whether to deploy APS as a standalone tool or as a native module within the MES.
Standalone APS tools often provide best-in-class optimization features. These are especially valuable in high-mix or constraint-heavy environments. However, they require custom integration into the MES and ERP systems. This involves mapping master data, synchronizing schedule changes, and building middleware to handle event-based updates. It also introduces latency between scheduling decisions and shop-floor actions.
In contrast, native APS modules within modern MES platforms are built on the same data model. This eliminates the need to duplicate data, reduces integration complexity, and allows the schedule to be adjusted the moment the MES detects a change. For example, if a machine fails or a quality issue arises, a native APS can immediately re-sequence the remaining work without needing to wait for a batch sync.
The trade-off is often functionality. Some integrated APS modules may initially lack the depth of algorithmic control offered by standalone tools. But MES vendors are closing that gap quickly. For many manufacturers, especially those standardizing on a platform for long-term digital transformation, the advantages of real-time responsiveness and lower integration costs outweigh the benefits of niche optimization features.
The Closed-Loop Advantage
The strategic value of integrating APS with MES is found in the creation of a closed-loop production system. APS generates a schedule, MES executes it, and the real-world results—actual cycle times, scrap rates, machine status—are fed back into the APS to refine future plans.
This loop enables dynamic adaptation. When conditions change, such as a late material delivery or unplanned downtime, the APS can revise the schedule to reflect new constraints. The revised plan is immediately dispatched to MES, ensuring operators work from current instructions.
Without this integration, manufacturers rely on manual interventions. Planners spend time adjusting schedules in spreadsheets. Operators work around problems based on tribal knowledge. Decisions are made with partial visibility. Integration removes these inefficiencies, replacing guesswork with real-time alignment.
The benefit is not just operational. From a business perspective, this improves on-time delivery rates, increases capacity utilization, reduces inventory buffers, and enhances customer confidence. In regulated industries, it also strengthens compliance by linking plans directly to execution and audit trails.
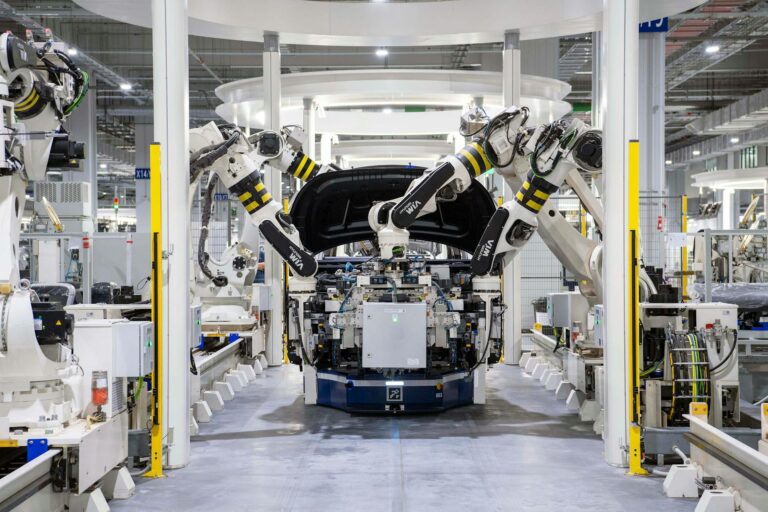
Architecture and Data Strategy
Achieving seamless APS-MES integration requires more than technical compatibility. It demands a coherent data strategy and system architecture.
When APS is separate from MES, the integration must bridge data models. Orders, routings, shift calendars, and equipment definitions must be kept synchronized. This is rarely perfect. Even minor mismatches can create issues, such as dispatching jobs to unavailable machines or exceeding real-world capacity.
A native APS avoids these problems by sharing the same database as MES. There is no need to transfer data or maintain separate records. When MES logs a production event, APS sees it immediately. This shared visibility is what enables real-time rescheduling and continuous optimization.
However, not all “integrated” systems are truly unified. Some vendors market bolt-on APS modules as integrated when, in fact, they operate on separate schemas or require API calls to exchange data. Buyers must conduct due diligence—asking whether the APS and MES share tables, execute in the same environment, and deliver a consistent user experience.
For those adopting best-of-breed tools, careful attention must be paid to data governance. Establishing a master data policy is essential. This includes designating system owners for each domain—materials, resources, routings—and defining how updates are propagated. Without this discipline, integration becomes brittle over time and undermines trust in the system.
Implementation Challenges and Organizational Alignment
Integrating APS and MES is not simply a software rollout. It involves process redesign, cultural change, and new roles for planners, operators, and supervisors.
Planners accustomed to static schedules must transition to managing dynamic priorities. Their role shifts from creator to curator—monitoring exceptions and using simulation tools to evaluate alternatives. This requires training and change management.
Operators need to trust that the schedule reflects reality. This is only possible if the integrated system enforces adherence and proves reliable. If instructions change unexpectedly or do not account for known constraints, users will revert to manual workarounds. Building trust takes time and requires visible wins.
Project teams should prioritize a phased rollout. A pilot line or product family can demonstrate value, uncover issues, and build internal advocacy. From there, the system can be scaled across plants or business units with confidence.
Governance is critical. A cross-functional steering committee should oversee the rollout, resolve conflicts, and maintain alignment between IT, operations, and planning. Data ownership must be assigned explicitly, and processes defined for continuous improvement. APS and MES are not static tools—they must evolve with the business.
Future State: AI and Digital Twins
Integrating APS and MES creates the foundation for more advanced capabilities. Artificial intelligence, machine learning, and digital twins are logical extensions of this platform.
With reliable MES data and a responsive APS, manufacturers can begin to layer predictive models on top. These might forecast maintenance needs, detect anomalies in process behavior, or suggest optimal batch sizes based on past performance.
A digital twin—a live simulation of the production process—becomes feasible when MES data streams into an intelligent planning model. This allows scenario analysis without disrupting actual operations. Planners can test the impact of a new schedule, a resource change, or a late order before committing.
These innovations rely on the integrity and granularity of the underlying data. If APS and MES are fragmented or loosely coupled, these capabilities cannot be realized. That’s why integration is not just about efficiency—it’s about strategic readiness.
Conclusion
APS and MES serve different functions but share a common purpose: delivering efficient, responsive, and predictable manufacturing operations. When implemented in isolation, each has value. But when integrated—especially in a native, real-time architecture—they become a transformative force.
This integration closes the gap between planning and execution. It enables a factory to respond dynamically to change, improve schedule adherence, and drive better business outcomes. It reduces reliance on spreadsheets and manual overrides. It builds trust across departments. And it lays the foundation for the next generation of intelligent manufacturing systems.
Manufacturers that invest in this integration—not just in tools, but in governance, data, and people—position themselves to lead in the era of smart factories and autonomous operations.