Introduction
A Manufacturing Execution System (MES) is often described as the digital backbone of modern manufacturing. But behind every MES lies a carefully designed software and hardware architecture—one that connects enterprise systems, shop floor equipment, and frontline operators. This article explores the foundational structure behind MES solutions and explains how a flexible, integrated MES architecture drives smart manufacturing forward.
As Industry 4.0 and digital transformation initiatives accelerate, understanding MES architecture is critical for operations leaders, engineers, and IT professionals seeking visibility, responsiveness, and compliance on the factory floor.
What Is MES Architecture?
MES architecture refers to the structural design of software components, integration layers, and interfaces that allow MES to manage and monitor production operations in real time. At its core, MES architecture provides a two-way bridge—linking high-level systems like ERP (Enterprise Resource Planning) with low-level control systems such as PLCs (Programmable Logic Controllers) and SCADA (Supervisory Control and Data Acquisition).
This architecture enables key MES functions: order execution, work instruction enforcement, traceability, data collection, and decision support. A scalable MES architecture allows manufacturers to adapt their production systems to changing demands, regulatory requirements, and continuous improvement strategies.
Historical Context: From MRP to Smart Manufacturing
MES emerged from earlier production systems such as MRP (Material Requirements Planning) and early shop floor control platforms in the 1980s and 1990s. These early systems lacked real-time capabilities and integration with machine-level data. As automation increased and production environments became more complex, the need for a unified execution layer became clear.
Organizations like MESA International and the ISA (International Society of Automation) helped formalize MES functionality. The MESA-11 model defined the core functions of MES, while ISA-95 established how MES integrates with other systems in the manufacturing stack.
Today, MES sits at the center of the smart factory, enabling closed-loop manufacturing, AI-driven decision support, and connected worker environments.
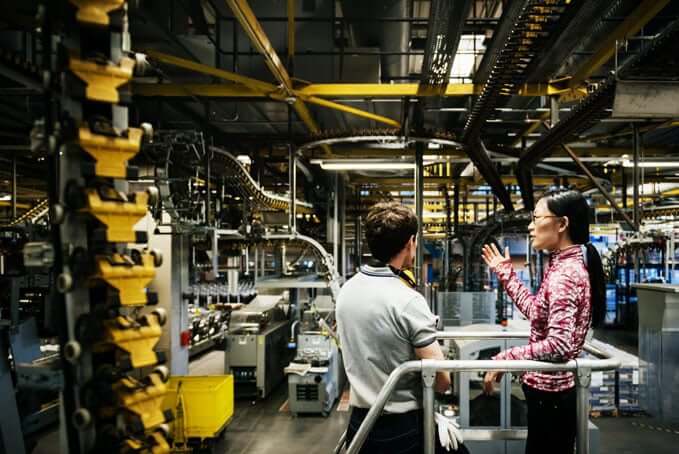
Core Layers of MES Architecture
Modern MES platforms are structured in logical layers, each responsible for a different aspect of production control and information flow:
1. Enterprise Layer
At the top of the stack, MES connects with business-level systems including ERP, PLM (Product Lifecycle Management), and QMS (Quality Management Systems). This layer is responsible for work order handoffs, bill of materials synchronization, master data exchange, and high-level reporting.
It allows ERP systems to issue work orders to the shop floor while receiving back real-time updates about production status, scrap rates, downtime, and quality metrics.
2. MES Platform Layer (Middleware)
This is the operational core. The MES platform manages job sequencing, resource allocation, work instruction enforcement, and traceability. It tracks parts and subassemblies, logs operator actions, records tool use, and verifies that steps are performed in the correct order.
The middleware layer translates enterprise instructions into execution tasks and consolidates execution data into a format that higher-level systems can interpret and analyze.
3. Control Layer
At the bottom, MES communicates with shop floor systems and hardware. This includes PLCs, HMIs, barcode scanners, vision systems, RFID tags, torque tools, and environmental sensors. Data collected at this layer provides the “shop floor truth” needed for real-time alerts, performance tracking, and root cause analysis.
Protocols like OPC UA, MQTT, and native drivers enable secure communication across diverse devices, even in legacy environments.
MES Deployment Models and Architectures
Modern MES platforms can be deployed in multiple ways depending on organizational needs, IT policies, and production environments. Each deployment model offers distinct benefits and considerations that influence performance, security, and scalability.
On-Premise MES
This traditional model involves hosting the MES software and data on servers located within the manufacturing facility. It gives the organization full control over system access, maintenance, and security.
Best for:
Manufacturers with strict data residency or regulatory compliance requirements
Environments with limited or unreliable internet connectivity
Companies with dedicated in-house IT infrastructure teams
Advantages:
Greater control over upgrades, backups, and access
Often better latency for real-time shop floor operations
Easier to connect with legacy equipment and local SCADA systems
Cloud-Based MES (SaaS)
Cloud MES platforms are hosted on external infrastructure (public or private cloud) and accessed via web interfaces or APIs. These are growing in popularity due to ease of setup and low IT overhead.
Best for:
Multi-site manufacturers who want centralized control
Facilities with robust internet connectivity
Organizations looking to avoid capital expenditure on IT infrastructure
Advantages:
Fast deployment and lower upfront costs
Easy to scale across new lines or locations
Frequent, automatic updates from the vendor
Accessible from anywhere (with proper permissions)
Hybrid MES
Some manufacturers combine cloud and on-premise elements to form a hybrid MES architecture. Core services may be hosted in the cloud, while time-sensitive machine data collection and processing occurs locally.
Best for:
Organizations transitioning to cloud
Manufacturers with global operations and site-specific constraints
Environments needing real-time responsiveness but central governance
Advantages:
Balance of speed, control, and scalability
Resilience in case of network outages
Easier integration with IT and OT systems across locations
Real-Time Control and Data Acquisition
One of the key advantages of MES is the ability to make decisions in real time based on data from machines and operators. This requires robust communication with:
PLCs to collect status and measurement data
SCADA systems to visualize and log signals
IoT sensors to capture torque, vibration, temperature, or pressure
Barcode and RFID readers to confirm material identity and routing
Operator interfaces (terminals, tablets, touchscreens) for task confirmation and data entry
By connecting these systems into the MES platform, manufacturers gain accurate, timestamped records of every step in the build process.
Enterprise Integration and Interoperability
A core strength of modern MES is its ability to integrate seamlessly with other enterprise systems, forming a connected manufacturing ecosystem. These connections are not just technical—they’re strategic, enabling automation, compliance, and optimization across the business.
ERP Integration
MES typically connects with ERP systems (like SAP, Oracle, or Microsoft Dynamics) to:
Receive work orders, BOMs, and routings
Provide production updates, scrap counts, and completion status
Sync inventory movements and material consumption
Integration occurs through RESTful APIs, middleware, or standardized message queues. This connection closes the loop between planning and execution, reducing manual handoffs and delays.
PLM Integration
MES benefits from integration with Product Lifecycle Management (PLM) platforms by:
Accessing the latest product configurations and design revisions
Applying variant-specific work instructions
Managing version-controlled build histories
This ensures engineering changes are implemented correctly at the workstation level—reducing errors and rework.
QMS and LIMS Integration
MES also communicates with Quality Management Systems and Laboratory Information Management Systems to enforce inspections, record test results, and document compliance.
Examples include:
Blocking progression if a quality check fails
Triggering CAPA workflows via QMS
Storing test data directly against work orders in MES
These connections make MES a hub for traceability and audit readiness.
BI and Analytics Platforms
Many manufacturers now link MES with business intelligence tools (like Power BI or Tableau) to visualize KPIs in real time. Dashboards help management monitor throughput, cycle times, and OEE across lines and facilities.
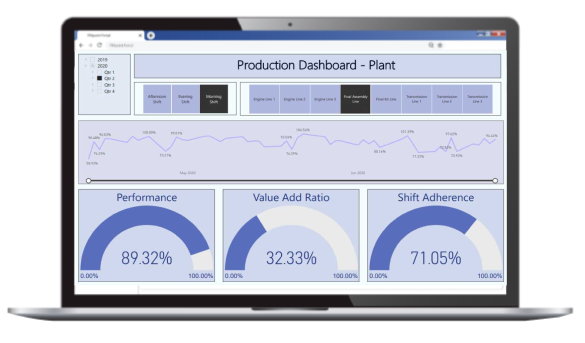
MES User Interfaces and Dashboards
The user experience layer plays a vital role in MES success. Operators interact with MES through:
Touchscreen HMIs at each station
Tablets or mobile devices on the line
Web-based dashboards for supervisors and engineers
Role-based views to match tasks and permissions
Alerts and guidance systems (lights, sounds, pop-ups) for escalation or deviation handling
A clear, consistent interface design reduces training time, lowers error rates, and increases confidence among production staff.
Design Best Practices for MES Architecture
Designing MES architecture requires strategic planning to support long-term business needs.
Modularity and Flexibility
Build the architecture using a modular approach. Start with foundational capabilities like job execution and traceability, and add more advanced features like OEE, SPC, or paperless quality as needed.
Interoperability
Choose platforms that support standard communication protocols and come with pre-built connectors or APIs for ERP, PLM, and SCADA systems. Avoid closed systems that create data silos or require custom integrations for every change.
Scalability
Design for scale—both vertically (across functions) and horizontally (across sites or regions). A plant-level MES should be able to evolve into a corporate-wide solution with consistent deployment models.
Cybersecurity and Resilience
Protect data flows between layers with secure protocols (HTTPS, TLS). Use edge computing or local buffering to protect against cloud or network outages.
MES and IT/OT Convergence
One of the most powerful roles MES plays in modern factories is unifying IT (Information Technology) and OT (Operational Technology)—two worlds that historically operated in silos.
MES as the Bridge
MES sits between business systems (like ERP or PLM) and equipment on the plant floor (PLCs, HMIs, CNCs, etc.). It’s the one layer that speaks both languages:
From IT: structured data, APIs, cybersecurity
From OT: real-time machine signals, low-latency execution, environmental feedback
By handling both layers, MES enables secure, scalable data exchange and coordinated decision-making from top floor to shop floor.
Why IT/OT Convergence Matters
Faster problem resolution: Real-time alerts trigger both IT and OT actions
Increased transparency: Shared data models and KPIs align operations with business goals
Streamlined compliance: Unified recordkeeping supports traceability and audit readiness
Predictive capabilities: Correlating machine data with planning systems supports AI and advanced analytics
Enabling Technologies
OPC UA, MQTT, and REST APIs
Edge computing to process data closer to the machine
Cybersecure gateways to protect cross-domain communication
MES architecture designed for convergence is key to future-proofing your operations in the age of smart manufacturing.
Common Pitfalls in MES Architecture
Not all MES implementations deliver results. Often, the issue lies not with the software—but with how the architecture is designed and deployed. Here are some common mistakes that can be avoided with better planning and execution.
1. Choosing a Rigid or Closed System
Some MES solutions lock customers into proprietary technology or limited integration paths. These rigid architectures make it hard to adapt to new machines, protocols, or business needs. Over time, the system becomes more of a barrier than a benefit.
Solution: Choose a platform that supports open standards, modular extensions, and integration flexibility.
2. Ignoring the Shop Floor Voice
MES is often led by IT or corporate functions, but without input from operators, engineers, and supervisors, the system may not reflect real workflows. This results in low adoption, bypassed instructions, and patchy data.
Solution: Involve cross-functional stakeholders early. Pilot the system with floor teams and gather feedback to refine workflows.
3. Underestimating Integration Effort
Connecting MES to ERP, PLM, SCADA, and QMS systems takes more than just plugging in APIs. Mapping data models, testing transaction flows, and aligning master data are complex tasks that require upfront planning.
Solution: Assign dedicated integration owners, use middleware where appropriate, and document all interface assumptions clearly.
4. Lack of Change Management
Even the best-designed system can fail if people aren’t trained, informed, and supported. Resistance often comes from fear of disruption, increased workload, or confusion.
Solution: Pair deployment with a communication plan, phased rollout, clear roles, and active support from leadership.
Case Studies: MES Architecture in Action
Automotive Tier 1 Supplier
A global Tier 1 automotive parts supplier implemented a modular MES with full integration to ERP and SCADA systems. They reduced rework by 25%, improved traceability, and met OEM compliance mandates for part-level serialization.
Medical Device Manufacturer
By integrating MES with QMS and ERP systems, a medical manufacturer enforced operator accountability and eliminated paper-based DHRs. Training time dropped by 40%, and they cut audit prep time by more than half.
Aerospace Assembly
A complex aerospace site needed part genealogy, variant tracking, and visual guidance. By aligning MES with PLM and quality systems, they achieved full traceability, reduced time-to-quality metrics by 30%, and accelerated their rate of continuous improvement.
Talk to PINpoint to get more information about these use cases or similar success stories for MES.
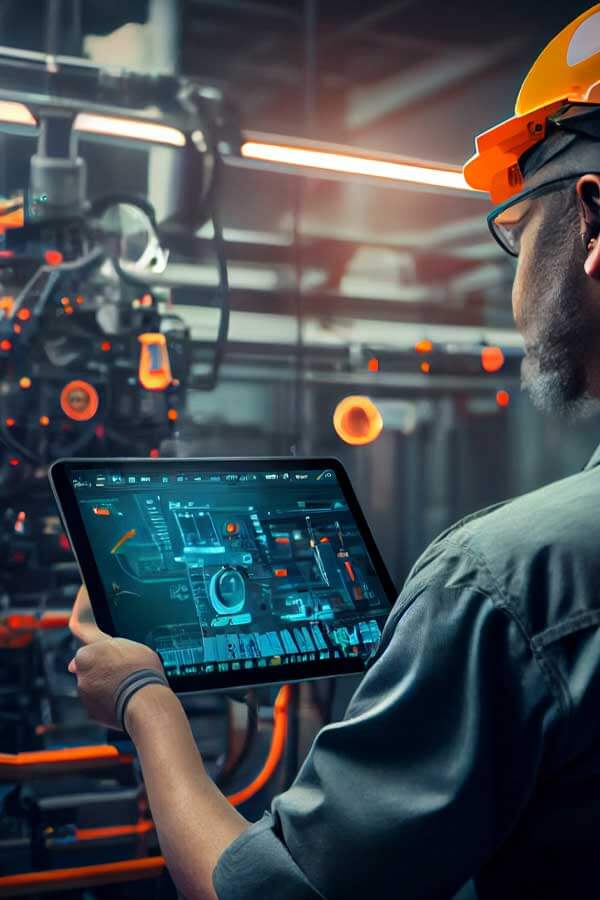
Future Trends in MES Architecture
AI and Predictive Analytics
MES will increasingly leverage machine learning to predict equipment failures, detect process drift, and suggest preventive actions based on real-time and historical data.
Edge Computing
By moving processing closer to the machines, MES can respond faster to events without relying solely on centralized infrastructure.
Augmented Reality and Digital Twins
MES interfaces will include AR tools for training, inspections, and remote collaboration. Digital twins of machines and processes will provide real-time simulation and predictive diagnostics.
Autonomous Manufacturing
Long-term, MES will support fully autonomous execution, where systems re-route production or adjust workflows without manual intervention, based on live sensor and system feedback.
FAQs
What is MES’s role in Industry 4.0?
MES enables real-time coordination between planning and execution. It delivers visibility, control, and integration—key elements of a connected factory.
How does MES integrate with ERP?
MES receives work orders, BOMs, and master data from ERP, and sends back execution status, scrap quantities, and shift performance data.
Can MES support legacy equipment?
Yes. MES can communicate with older machines using OPC UA gateways, retrofit sensors, or digital I/O signals converted by edge devices.
Conclusion
MES architecture is what makes real-time manufacturing possible. It connects machines, systems, and people in a way that allows continuous monitoring, quality enforcement, traceability, and improvement.
As manufacturing evolves, so must MES. The right architecture allows a plant to scale, adapt, and compete in a digital-first, data-driven industry.