Introduction
MES Vs QMS? Manufacturers looking to improve quality, reduce defects, and meet compliance goals often evaluate both Manufacturing Execution Systems (MES) and Quality Management Systems (QMS). These two systems share overlapping goals, but they are not the same. Confusing them—or choosing one when both are needed—can lead to missed opportunities and inefficiencies on the factory floor.
This article explains the difference between MES and QMS, how they complement each other, and what manufacturers should consider when investing in either system.
What is a QMS? A Quick Refresher
A Quality Management System is a formal structure of policies, procedures, and processes that guide how a company manages and improves quality. It defines how quality is built into the product at every stage, from planning to production to delivery. Read our article ‘What is a Quality Management System (QMS)?‘ for a more detailed explanation, but in summary, a QMS ensures that:
Requirements are defined and documented
Processes are standardized and controlled
Non-conformances are recorded and resolved
Records are maintained for compliance and audits
Continuous improvement is part of daily operations
A QMS is typically aligned with international standards like ISO 9001, IATF 16949, or FDA 21 CFR Part 820, especially in regulated industries.
But while a QMS defines what needs to happen and why, it doesn’t always enforce how it happens during production. That’s where MES comes in.
What is an MES?
A Manufacturing Execution System is a software platform that controls, monitors, and documents what happens on the shop floor in real time. MES is focused on the execution of manufacturing activities.
It tells operators what to do, when to do it, and how to do it—based on product configuration, part availability, and process status. It also captures data as tasks are completed.
An MES typically includes:
Digital work instructions
Operator guidance
Machine and tool integration
Real-time production tracking
Automatic enforcement of process sequences
Traceability of materials, people, and equipment
Quality checks during execution
Where QMS focuses on the framework for quality, MES ensures it’s executed correctly, every time.
Read our article ‘MES 101: What is a Manufacturing Execution System‘ to learn more about Manufacturing Secution Systems, or visit our product pages to learn about the PINpoint MES.
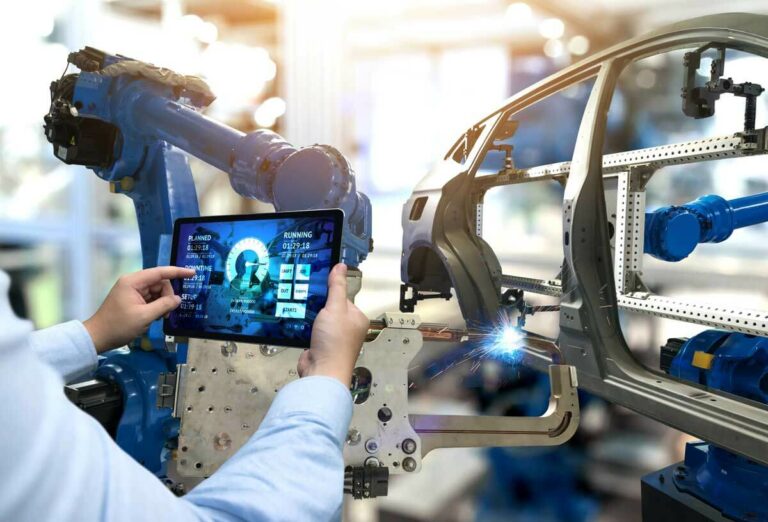
MES Vs QMS: The Key Differences
Let’s compare these two systems side by side:
- QMS
- MES
QMS | MES | |
Purpose | Manage quality policies, documentation, and compliance | Execute and track manufacturing processes in real time |
Focus | Product and process quality | Shop floor execution |
Core Functions | Document control, CAPA, audit management, SOPs | Work instructions, real-time data collection, task enforcement |
Users | Quality managers, compliance teams, auditors | Operators, supervisors, engineers |
Data Collected | Non-conformance reports, audit trails | Real-time operator actions, tool data, inspection results |
Automation | Workflow approvals, form routing | Step sequencing, tool integration, auto-validation |
While MES and QMS serve different functions, they work best when integrated.
Where the Systems Overlap
There are areas where MES and QMS intersect—particularly around quality assurance, traceability, and compliance. For example:
MES can enforce process steps and collect inspection results that are required by the QMS.
QMS may define the criteria for pass/fail conditions, but MES ensures those criteria are verified in real time.
MES provides the data that QMS uses for reporting and auditing.
QMS initiates CAPA events when an issue occurs; MES helps identify the root cause using traceability data.
MES Vs QMS? Both systems are essential for a complete digital quality strategy.
When to Use QMS Alone
Some manufacturers, especially smaller ones or those in contract manufacturing, may begin with a QMS platform to establish basic documentation and audit readiness.
A standalone QMS may be sufficient when:
You are focused on document control and regulatory compliance
Production is stable, low-volume, and low-mix
You don’t need automated guidance or in-line inspection
Manual records and paper-based instructions are acceptable
In these environments, QMS supports quality planning but may not capture execution-level data.
When MES is the Better Fit
For manufacturers managing complex assemblies, multiple product variants, or high-mix production lines, MES delivers real-time control that QMS alone cannot provide.
You likely need MES when:
Work instructions change by product configuration or station
You need to enforce task order and prevent skipped steps
You require traceability for people, parts, and tools
You want automatic validation of operator inputs or measurements
You need to reduce training time with guided workflows
MES turns the quality policies defined in the QMS into real-time instructions on the factory floor. It helps ensure that the plan is followed every time, by every operator.
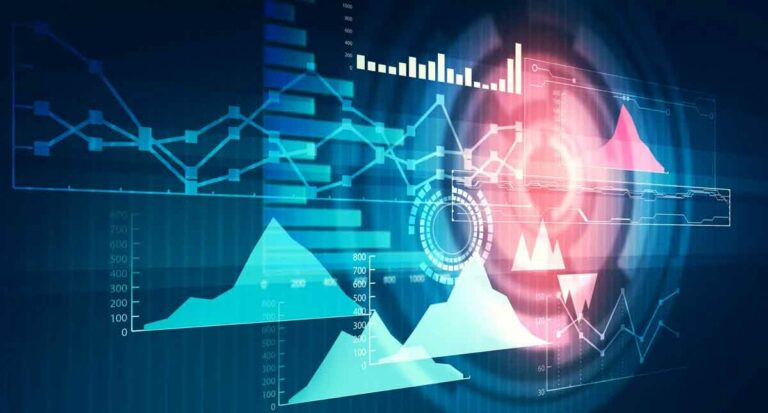
Why Manufacturers Need Both
Don’t think MES Vs QMS. A Manufacturing Execution System (MES) and a Quality Management System (QMS) are not competing solutions—they are complementary technologies that serve distinct roles. A QMS sets the framework for quality: it defines standards, procedures, and goals. It ensures that the organization has documented expectations for how work should be done and how quality should be measured. However, the QMS alone does not enforce these processes on the shop floor.
This is where MES provides critical support. An MES is responsible for operationalizing the quality policies and procedures defined in the QMS. It provides digital work instructions, step-by-step guidance, and automated controls to ensure that operators perform tasks correctly. MES systems also capture real-time production data, making it possible to confirm that each process was followed precisely, every time.
When MES AND QMS are used together, manufacturers can define expectations at the policy level, enforce them during execution, and collect data for ongoing evaluation and improvement. MES ensures that tasks are performed correctly. QMS ensures that the overall system evolves and improves. When integrated, these systems provide a closed loop that connects planning to execution and feedback to strategy.
Integration Benefits
Integrating MES and QMS systems provides several advantages:
Faster CAPA Resolution
MES provides the real-time traceability needed to isolate where an error occurred. This supports faster root cause analysis and corrective action in the QMS.
Better Audit Readiness
When MES and QMS are connected, audit trails are complete and consistent—from the process definition to the execution and inspection data.
More Accurate Quality Metrics
MES captures granular, time-stamped data. Feeding this into the QMS enables better reporting on quality KPIs like first-pass yield, rework rate, or defect frequency.
Closed-Loop Improvement
With MES collecting data and QMS analyzing it, manufacturers can continuously improve both execution and oversight processes.
Example Scenarios
In the medical device industry, manufacturers must comply with strict FDA regulations such as 21 CFR Part 820. The QMS handles the documentation, change control, and audit trail requirements, ensuring that procedures are followed and documented. The MES complements this by guiding operators through validated workflows, capturing data for Device History Records (eDHR), and enforcing in-process quality checks. Together, these systems ensure compliance and traceability from start to finish.
In automotive manufacturing, QMS platforms are used to manage compliance with IATF 16949, particularly around supplier quality, audits, and corrective actions. MES systems play a different but equally important role—they are responsible for real-time error-proofing, sequencing operations, and confirming that each product variant is built to specification. The combined system helps manufacturers avoid costly recalls and meet customer quality expectations.
For electronics assembly, speed, precision, and process control are critical. The QMS defines inspection criteria, escalation paths, and corrective action procedures. The MES ensures that these criteria are met during production. It can pause workflows if an operator misses a step or if a test value falls outside specification. Engineers and quality managers can use this data to resolve issues faster, prevent recurrence, and refine both systems over time.
MES Vs QMS: Conclusion
MES and QMS are not interchangeable systems—they serve different but complementary purposes. A QMS helps you define and manage quality across the organization. An MES helps you enforce and monitor those definitions on the shop floor.
To meet today’s quality, traceability, and compliance demands, manufacturers need both systems working in sync. MES ensures that every task is done correctly, while QMS ensures that the system keeps improving.
When integrated, they provide the full visibility, control, and accountability needed to drive world-class manufacturing performance.