Introduction to Manufacturing Work Instructions
Manufacturing work instructions are detailed, step-by-step guides that explain how to carry out specific tasks on the shop floor. These documents convert general procedures into actionable directions. When used correctly, they ensure consistent quality, reduce training time, and support safety in day-to-day operations. In this article, we break down what work instructions are, the different types used in manufacturing, the core components of effective instructions, and how modern technologies are changing the way they’re created and used.
Definition and Purpose of Work Instructions
Work instructions tell operators exactly how to complete a task. Unlike procedures, which describe what to do and who does it, work instructions explain how to do each step. This distinction is critical. A procedure might say “assemble the gearbox,” while a work instruction tells the operator to “insert bearing A into housing B using press tool #105.”
Their main purpose is to standardize tasks across the factory. Standardization ensures each product is built to the same specification. This lowers defect rates and reduces variation between shifts and locations. When everyone follows the same method, problems are easier to find and fix. It also improves training: new workers can follow instructions without relying on tribal knowledge. A good instruction is easy to follow and includes the right level of detail to avoid errors.
Safety is another key reason for work instructions. Many workplace accidents result from system errors, such as unclear or missing instructions. Documenting steps and safety precautions helps reduce risk. In complex production environments, clear instructions are essential to meet customer expectations and safety requirements.

Types of Work Instructions
Manufacturers use different types of work instructions depending on the task and the needs of the operator. Here are the main formats:
Text-Based Instructions: The most common format, especially for simple tasks. These instructions list steps using short, clear sentences. Good textual instructions use active voice and a consistent tone. They are often enhanced with numbering and clear formatting to improve readability.
Visual Instructions: These include images, diagrams, or illustrations. Pictures can show complex sequences or clarify spatial orientation. According to MESA International, including visuals improves comprehension and reduces errors. Visual instructions are helpful in multilingual environments or when tasks involve manual dexterity.
Checklists and Job Aids: For tasks with verifications or repeated checks, a checklist format works well. These help ensure no steps are missed and that every requirement is met. Common in quality control, maintenance, and inspections.
Video and Multimedia Instructions: Some manufacturers create videos to show how to perform tasks. These are especially useful for complex processes where motion or timing matters, such as welding or assembling intricate parts.
Interactive Digital Instructions: These run on tablets or screens and guide the user step-by-step. Operators can confirm actions, input measurements, or be redirected based on conditions. These instructions support real-time validation and integrate with other systems like MES.
Augmented Reality (AR): AR-assisted instructions overlay digital cues on real-world objects using smart glasses or tablets. For example, an AR system might highlight which part to pick or where to place it. Boeing reported an 88% improvement in first-pass accuracy using AR-guided wiring assembly.
In practice, many companies use hybrid formats: combining text, images, and video, or offering both paper and digital versions depending on the station and operator skill level.
Core Components of Effective Work Instructions
To be useful, a work instruction must be clear, accurate, and easy to use. These are the components that make them effective:
Title and Identification: Each instruction should have a clear title and document code. It should also include a revision number and approval information to ensure the right version is in use.
Purpose and Scope: A short description that explains what the instruction covers and where it applies. This helps distinguish similar instructions and ensures it’s used correctly.
Step-by-Step Procedures: The main body includes the sequence of tasks. Each step should describe a single action using simple, direct language. Numbering helps users follow along and refer to specific points. Where needed, the step can include a short rationale to explain why it matters.
Safety Warnings: Call out any risks or required precautions. Use standard icons and clear labels for steps that involve hazards. For example, “CAUTION: Wear gloves when handling hot parts.”
Tools and Materials: A list of everything the operator needs to complete the job. This prevents delays and ensures tasks are completed using the right equipment.
Quality Criteria: Instructions should include pass/fail criteria, tolerances, or checkpoints. These guide the operator on what “done right” looks like and support self-inspection.
Visual Aids: Photos, diagrams, or charts clarify the text. A good visual shows exactly what the operator should see or do. Visuals are especially helpful when explaining orientation, fit, or assembly sequence.
Formatting and Language: The document should use readable fonts, consistent terminology, and avoid jargon. Layout matters: use spacing, numbering, and headings to make scanning easy. Write at a Grade 8 reading level unless technical terms are needed.
Accessibility: Instructions must be easy to find and use. In paper-based environments, they should be posted at workstations. In digital systems, users should be able to scan a barcode or select the task to bring up the correct instruction.
Maintenance and Updates: Work instructions must be current. Any change to a part, process, or tool should trigger a revision. A good instruction system includes version control and assigns responsibility for keeping documents up to date.
Benefits of Work Instructions
Good work instructions produce measurable gains in quality, safety, training, and compliance. Here’s how:
Better Quality and Consistency: Standardized instructions reduce variation. According to VKS, using digital work instructions helped one electronics manufacturer reduce defects and increase productivity by 20%. Boeing reported up to 90% improvement in first-pass yield when using AR guidance.
Faster Training: Instructions serve as built-in training material. New workers can follow documented steps without shadowing an expert. CMP Advanced Mechanical Solutions reported a 50% faster training time with digital instructions.
Improved Safety: By clearly stating safety steps, PPE requirements, and hazard warnings, instructions help reduce injuries. OSHA encourages written procedures for all safety-critical tasks.
Less Reliance on Memory: When steps are written down, operators don’t need to memorize complex tasks. This supports cross-training and reduces risk when key personnel are unavailable.
Stronger Compliance: In regulated industries, work instructions are mandatory. ISO 9001, IATF 16949, and FDA 21 CFR Part 820 all require documented, controlled procedures. Digital instructions also simplify audits by showing what was done, by whom, and when.
Enabling Continuous Improvement: With standardized steps in place, companies can analyze performance, make improvements, and roll out updates. Digital systems can track how long each step takes or how often steps are skipped, helping identify bottlenecks or training gaps.
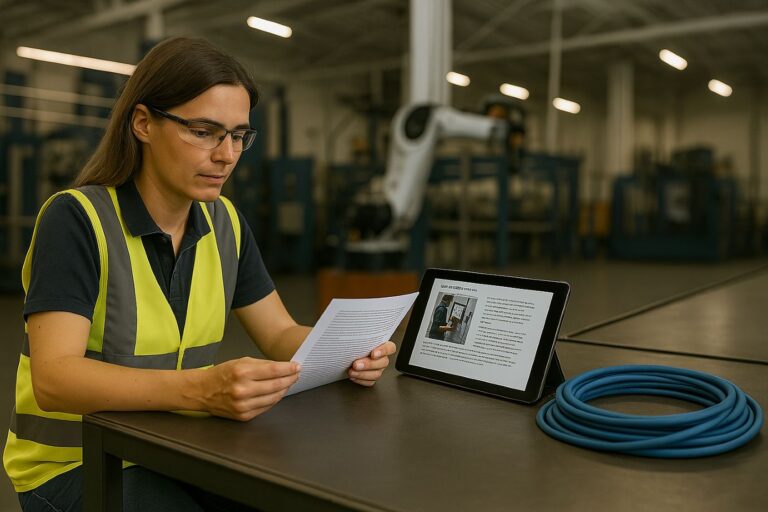
Industry Trends and Digital Transformation
The role of work instructions is changing with the rise of digital manufacturing. Several trends are reshaping how they are delivered and used:
From Paper to Digital: Many factories are replacing printed documents with digital systems. Digital instructions are easier to update, can include rich media, and are accessible at the point of use. Updates happen instantly and reach all users.
Tablets and Mobile Devices: Tablets mounted at workstations or issued to workers allow fast access to instructions. Operators can zoom in on images, play short videos, or confirm steps in real time. This format is intuitive and suits today’s digital-native workforce.
Integration with MES and IIoT: Work instruction platforms are being integrated with Manufacturing Execution Systems (MES). This means that instructions can change automatically based on the order, part number, or station. Sensors and smart tools can also confirm when a step is completed, enabling real-time tracking.
AR and Projection Systems: Augmented Reality is being used to overlay instructions directly onto the work environment. For example, a projector can light up the correct bin for picking, or a headset can show a 3D model of how parts fit together. This reduces the need to look away from the task and can eliminate errors.
Analytics and Feedback Loops: Modern instruction systems collect data. Managers can see which steps take longest, where errors happen, and whether instructions are being followed. This supports continuous improvement and faster troubleshooting.
Personalized Instructions: Systems can adapt instructions based on the user’s experience level, language, or preferences. A new hire might see more detail and reminders, while an expert sees a streamlined checklist.
Connected Workflows: Instructions now tie into broader systems. Completing a task might trigger a quality check, send data to ERP, or notify a supervisor. This integration helps maintain flow and ensures that every step is logged.
Conclusion
Work instructions are the foundation of consistent, high-quality manufacturing. They translate planning into execution and connect engineering intent with shop floor action. By documenting the best way to perform a task, they reduce errors, support training, and ensure compliance.
Modern manufacturing demands more than a laminated sheet on a clipboard. Today’s factories are moving toward digital, visual, and interactive instructions that guide and verify every action. Whether in a high-mix assembly line or a regulated cleanroom, effective work instructions matter. They are not just a quality tool—they are a strategic asset.
The next step is understanding how Manufacturing Execution Systems enhance the creation, delivery, and tracking of these instructions. Read about what is possible and in the follow-on article: “How MES Improves Manufacturing Work Instructions: Insights and Case Studies.”