What Is A Manufacturing Execution System (MES)?
A Manufacturing Execution System (MES) is essential software that monitors, guides, and controls factory operations in real time. It connects business-level planning systems like ERP with the machines, workers, and sensors on the shop floor. In doing so, MES ensures that production runs smoothly, quality checks are enforced, and decisions are based on accurate data. This article introduces MES and explains why it plays a vital role in modern discrete manufacturing.
A Brief History of MES
Manufacturing Execution Systems started evolving in the 1980s as manufacturers moved beyond spreadsheets and basic automation. By the early 1990s, the term “MES” became widely used to describe systems that controlled real-time factory operations. In 1997, the Manufacturing Enterprise Solutions Association (MESA) defined 11 core functions of MES, setting a standard for the industry. Soon after, the ISA-95 model positioned MES at Level 3 between enterprise systems (Level 4 ERP) and plant-floor control (Levels 0-2).
Today, MES has become a key enabler of Industry 4.0. It supports digital manufacturing, integrates with cloud and IoT systems, and helps factories move toward real-time, data-driven decision-making.

Core Functions of Manufacturing Execution Systems
Modern MES platforms perform several essential roles in manufacturing. One of the most important is scheduling and dispatch. MES takes high-level plans from ERP systems and generates detailed schedules. These schedules are then broken down into work orders, which are assigned to machines or operators in real time, based on priorities and resource availability.
The system also manages work order execution by delivering digital instructions to operators. As each task is completed, the MES tracks progress, giving managers a live view of work-in-progress. At the same time, MES interfaces with machines and sensors, capturing performance data such as cycle time, machine uptime, and maintenance alerts. This equipment integration allows MES to adjust production dynamically and avoid bottlenecks.
Quality control is embedded within the system, prompting operators to perform checks and logging the results. If measurements fall outside limits, the system flags the issue. This ensures problems are addressed quickly and helps meet industry standards such as ISO and FDA compliance.
MES tracks every component, machine, and action involved in building a product. This is known as traceability. If a problem arises later, MES can show exactly which materials and processes were used. This level of detail is essential for recalls and audits.
The platform also measures performance through Overall Equipment Effectiveness (OEE). It tracks metrics like downtime, scrap, and cycle time, helping managers pinpoint areas for improvement. MES supports inventory control by monitoring raw materials, triggering replenishment alerts, and ensuring the right parts are available on the line. All of these functions rely on accurate data collection and reporting, which the MES automates across the production process.
Why MES Matters
Ultimately, it comes down to cost savings. Proper implementation of a good MES will generate savings in several areas. Less waste, more efficient use of labor, and improved scheduling all contribute to lower expenses. In one documented case, a factory saved $400,000 in a single year by using a PINpoint system to identify and fix inefficiencies.
An MES makes a major difference to factory performance by improving overall productivity. When operators and managers have real-time information, they can respond faster to issues, finding ways to optimize processes and removing bottlenecks. In some cases, manufacturers have increased production output by 30% and boosted machine utilization by 95% after adopting MES.
Quality also improves. MES enforces checks at the right times and stops incorrect steps. By catching errors early, it reduces scrap and rework. The digital records it creates help prove compliance during audits and make root-cause analysis faster.
Decision-making is another area where it can add value. Instead of waiting for end-of-shift reports, supervisors can view dashboards that show what’s happening now. This helps them take action quickly when performance drops or problems emerge.
MES also enables increased agility in factories. When a new product is introduced or a custom order arrives, MES helps teams switch over quickly. Updated instructions can be sent digitally to all stations. This reduces downtime and avoids miscommunication.
Improved compliance can be achieved by automatically creating an electronic history of each unit built. Industries with strict regulations—such as aerospace, pharmaceuticals, and food—use MES to meet traceability and documentation standards. This improves safety, reduces legal risk, and makes inspections easier.
Finally, the increased visibility offers cannot be overstated. Real-time data lets managers see production status, machine speeds, and quality trends. With this insight, they can optimize operations continuously.
Real-World MES Examples
Across many industries, Manufacturing Execution Systems play a critical role. In automotive manufacturing, MES tracks each component and step in the assembly process, reducing the risk of recalls. In aerospace, it ensures that all materials and processes meet regulatory standards. Pharmaceutical manufacturers use MES to maintain electronic batch records that comply with FDA rules. Electronics companies benefit from MES during frequent product changeovers, where fast and accurate updates are essential.
Some large manufacturers have achieved substantial results. For instance, Cooper Tire were able to standardize processes across plants, leading to lower costs and better product quality.
Implementation Challenges
Despite its benefits, implementation can be challenging, especially if you don’t select the right platform or the right partner. Upfront costs can be high with less modern MES platforms, were custom integration or configuration can be difficult. Unless using a platform built with integrations in mind, connecting MES with ERP systems, legacy machines, and other software can take time and require skilled resources.
Change management is another hurdle. Introducing MES alters how people work. Some operators may resist using new tools, especially if they are used to paper-based systems. To succeed, companies must invest in training and explain how MES helps everyone do their jobs more easily.
System downtime during installation is a risk. If MES doesn’t function as expected during rollout, production could suffer. To avoid this, companies often test the system on a pilot line before full deployment.
Once installed, MES requires ongoing maintenance. It must be kept current and adapted to evolving processes. Poor configuration can add unnecessary tasks or create bottlenecks. Security is also a concern, since MES holds sensitive data and must be protected from cyber threats.
Nevertheless, the long-term gains usually outweigh the effort. More vendors now offer modular, cloud-based MES solutions that reduce setup time and cost. These systems are more scalable and easier to support, making the benefitcs accessible even to smaller manufacturers.
Looking Ahead - The Future Of Manufacturing Execution Systems
MES is evolving with new technologies. Cloud-based systems offer greater flexibility and easier updates. Factories can scale across multiple locations without building complex IT infrastructure.
Integration with Industrial Internet of Things (IIoT) devices is giving MES access to richer, real-time data. Machines can report performance metrics, energy use, and wear conditions directly to MES. This helps trigger maintenance before breakdowns occur and improves production planning.
Artificial intelligence and advanced analytics are starting to shape the future of MES. These tools help predict quality issues, suggest better workflows, and provide intelligent alerts. MES is becoming not just a control system but a decision support platform.
Modern interfaces are also becoming more user-friendly. Mobile apps allow managers to check production from anywhere. Augmented reality tools can overlay digital instructions on real equipment, guiding technicians through complex tasks.
Looking forward, MES will continue to be the foundation of smart manufacturing. As more factories adopt Industry 4.0 practices, MES will tie together the machines, people, and processes into one connected system. Analysts project strong growth in the MES market, with adoption rising steadily through 2030.
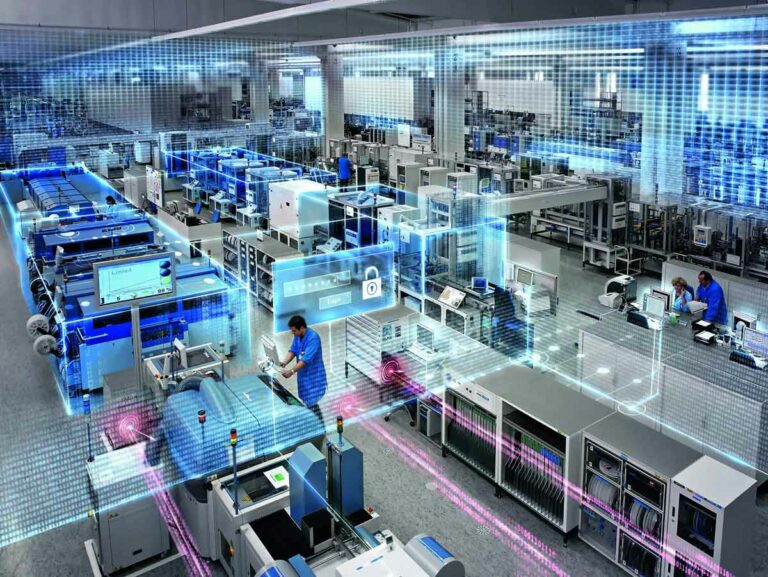
Conclusion
A Manufacturing Execution System is the core of digital manufacturing. It connects planning and production, ensures quality, tracks performance, and helps teams make better decisions in real time. While implementation takes effort, the gains in efficiency, quality, and agility make it a valuable investment.
For manufacturers looking to stay competitive, MES is not optional—it’s essential. It provides the structure, insight, and flexibility needed to succeed in a fast-changing, technology-driven world.