What Is MES in Discrete Manufacturing?
In discrete manufacturing, parts are put together to make things like vehicles, electronics, and machines. A Manufacturing Execution System (MES) is software that helps manage these operations from start to finish. It connects planning systems like ERP with equipment like PLCs and sensors on the factory floor.
The main purpose of MES is to take work orders from planning systems and make sure the right tasks happen in the right order. It also collects real-time data from machines and people. This helps track progress, control quality, and make production smoother.
A good MES should link to systems at all levels. It helps get the right materials to the right place, guides workers, and collects data on what happens during production. This keeps work on schedule and improves performance. Here are ten specific ways MES improves discrete manufacturing.
1. Real-Time Production Visibility and Control
MES gives workers and managers live updates on what’s happening. They can see which orders are running, where delays are, and if machines are idle. If something goes wrong, MES can send alerts right away. This lets supervisors fix problems fast.
Real-time visibility provides actionable insights that help reduce production surprises. Supervisors can respond to quality defects, equipment issues, or material shortages before they escalate. According to MESA International, manufacturers using MES improved their on-time delivery rates by an average of 22%. With MES dashboards and alerts, it becomes easier to keep production aligned with delivery schedules.
A Manufacturing Execution System also enhances customer satisfaction. When every order is tracked in real time, planners can give accurate delivery estimates. Operators know exactly what to produce and when, reducing confusion. The transparency also supports better inventory accuracy. With MES tracking WIP and finished goods, businesses avoid late shipments caused by missing parts or undocumented stock.
Moreover, the system gives production managers tools to make informed decisions quickly. They can adjust task assignments, reroute jobs, or change schedules to meet new priorities. In discrete environments where customer demands shift rapidly, that kind of agility supports both responsiveness and profitability.
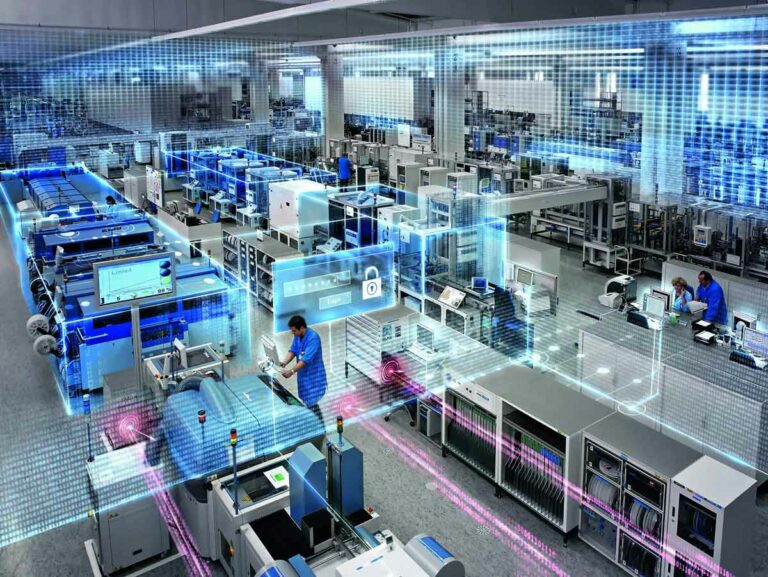
2. Higher Throughput and Efficiency
MES helps teams do more with the same machines and workers. It does this by cutting wait times, removing extra steps, and lining up jobs in a smart way. In one factory, MES shaved 50 seconds off each station by spotting a manual check that could be automated. That small saving added up to 10 extra units per day and $400,000 saved per year (PINpoint Case Study).
These improvements are not isolated. LNS Research found that MES adopters see an average 20% to 30% improvement in overall production efficiency. By analyzing production data and optimizing workflows, manufacturers can identify and fix hidden inefficiencies that traditional systems overlook.
Another key efficiency gain comes from tracking Overall Equipment Effectiveness (OEE). MES systems break down OEE into availability, performance, and quality. This helps teams find where time is being lost, whether due to long setup times, frequent stoppages, or substandard parts. Real-time metrics enable continuous improvements at the equipment and operator level.
Firms that use comprehensive MES platforms—not just for scheduling but also for analytics and process enforcement—have reported as much as 49% higher Takt time compared to those without MES. That means faster cycle times and more output per hour without hiring more staff or buying new machines.
3. Improved Product Quality and Defect Reduction
MES makes sure quality checks happen at the right time. It won’t let operators skip steps or use the wrong parts. For example, it might require a torque value to be logged or a serial number to be scanned before moving to the next step.
Built-in quality enforcement ensures that mistakes are caught early, reducing scrap and rework. According to McKinsey, using real-time analytics to monitor production quality can lower defect rates by up to 40%. A Manufacturing Execution System systems can enforce pass/fail checks, ensure correct component usage, and even prevent machines from operating if input conditions are outside tolerance.
Additionally, MES helps eliminate manual data entry errors. By pulling data directly from sensors and test equipment, MES ensures that quality data is accurate and timely. This also makes it easier for quality teams to identify trends. For instance, if defect rates spike during a particular shift or at a specific workstation, MES data can help engineers find the root cause.
The results are measurable. According to MESA, companies that implement MES often see their net profit margins improve by nearly 19.4%, due in part to fewer defects and lower warranty costs. MES systems support statistical process control (SPC) and provide automated alerts when metrics drift outside acceptable ranges.
This focus on quality is especially important in regulated industries like aerospace, automotive, and electronics, where the cost of defects can be extremely high. MES provides traceability and audit trails that prove compliance and support continuous improvement.
4. Reduced Downtime and Higher OEE
Machine downtime hurts productivity. MES helps by giving early warnings when equipment slows down or stops. It tracks usage so maintenance can be done before problems occur. Plants using predictive maintenance have seen 30% to 50% less downtime (McKinsey).
MES also speeds up changeovers. It prepares the next set of instructions and materials so workers don’t waste time. Over time, the MES builds a record of why stoppages happen. This helps the team make smart changes that increase equipment availability.
5. Optimized Inventory and WIP Levels
MES gives real-time tracking of parts and products at each stage. It sends alerts if materials are low and prevents overproduction. This keeps inventory levels lean and avoids pileups on the floor.
It helps maintain just enough stock without shortages. Plants using MES report higher inventory turns and reduced WIP. This frees up cash and floor space, helping the business run more efficiently.
6. Standardized Processes and Repeatability
MES makes sure every worker follows the same steps. When someone logs into a station, they see specific instructions, and the system won’t let them skip important actions. This reduces errors and makes sure each product is made the same way.
This process enforcement builds consistency. In a discrete plant with hundreds of parts and steps, small mistakes can lead to costly rework. MES prevents that by guiding workers through each task and requiring digital confirmation that steps are completed correctly.
For example, a Manufacturing Execution System can verify that tools are calibrated, that operators are certified, and that the correct component is used for each build. One provider of MES systems, reports that manufacturers using digital work instructions and MES-guided tasks see a drop in operator errors and less need for rework.
This standardization improves not just quality but also training. New employees can follow step-by-step instructions without relying on memory or tribal knowledge. Over time, this lowers onboarding costs and reduces dependency on senior staff.
MES also supports product genealogy. Every action and measurement is stored, creating a digital birth record for each product. If a problem is found later, manufacturers can trace it back to the exact process step, tool, and operator. This traceability is essential for quality audits and managing recalls.
Ultimately, MES ensures that every product is built to the same standard, every time. That repeatability increases reliability and builds customer trust.
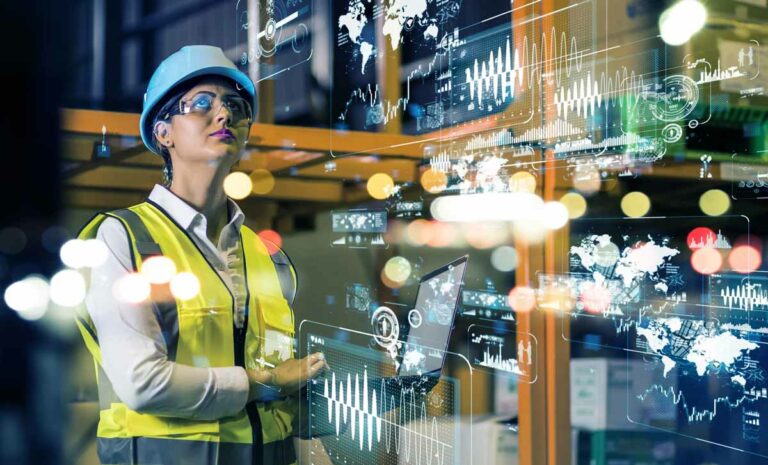
7. Data-Driven Continuous Improvement
A Manufacturing Execution System records data from every task. Managers use this data to find and fix problems. For example, if one station is always slower, MES can help investigate why.
Some systems use AI to suggest process changes. Over time, this leads to steady performance improvements. MES supports teams that want to make small improvements each day. It gives them the facts they need to test changes and measure results.
8. Empowered and Engaged Workforce
MES helps workers do their jobs better. It gives them live updates, digital work instructions, and tools to report problems. This reduces guesswork and paperwork. Operators can see their progress and feel more in control.
Some companies use MES dashboards to create friendly competition. This boosts morale and output. Workers also share tips through MES systems, so everyone learns from each other. Overall, it builds a culture of accountability and pride in work.
9. Improved Planning and Scheduling Accuracy
MES connects planning with what’s really happening. It helps make schedules that reflect current machine status, material availability, and labor. When orders change, MES adjusts the plan and sends updates to the floor.
This reduces overtime, cuts idle time, and shortens lead times. Some companies report getting a week’s worth of work done in four days after MES. With MES, planners can trust that what they schedule will actually happen.
10. Paperless Operations and Better Data
MES replaces paper with digital tools. Operators get electronic work instructions, log data directly into the system, and access records instantly. This reduces errors and saves time.
It also makes audits easier. Every action is time-stamped and signed digitally. Plants avoid lost paperwork and speed up compliance checks. Over time, digital records help improve traceability, decision-making, and cost control.
The Bottom Line
A good Manufacturing Execution System is more than just software. It helps plants (and their people) build better products, faster and at lower cost. It improves everything from quality to inventory, planning, and teamwork. By using MES, manufacturers can meet today’s demands and prepare for future changes with confidence.
As technology evolves, MES will continue to add new tools like AI, IoT, and cloud platforms. But its core value stays the same: giving the shop floor the control, insight, and structure it needs to perform at its best.